Sheet metal stamping process
Typically, the three most important steps in a sheet metal factory are shearing, punching/cutting, and folding. Modern sheet metal processes include: filament power winding, laser cutting, heavy duty machining, metal bonding, metal drawing, plasma cutting, precision welding, roll forming, sheet metal bending, die forging, water jet cutting, etc.
In 3D software, SolidWorks, UG, Pro/E, SolidEdge, TopSolid, etc. all have sheet metal parts, mainly through the editing of 3D graphics to obtain the data required for sheet metal parts processing (such as unfolding drawings, bending lines, etc. ) and provide data for CNC Punching Machine / Laser, Plasma, Waterjet Cutting Machine (Laser, Plasma, Waterjet Cutting Machine) / Combination Machine and CNC Bending Machine, etc.
Sheet metal quality inspection
In addition to the strict requirements in the production process, the quality of sheet metal parts requires quality inspection independent of production. One is to strictly control the size according to the drawings, and the other is to strictly control the appearance quality. If the size does not match, it will be repaired or scrapped. Scratches are allowed, and the color difference, corrosion resistance, adhesion, etc. after spraying are inspected. In this way, you can find errors in the unfolding diagram, bad habits in the process, errors in the process, such as digital punch programming errors, mold errors, etc.
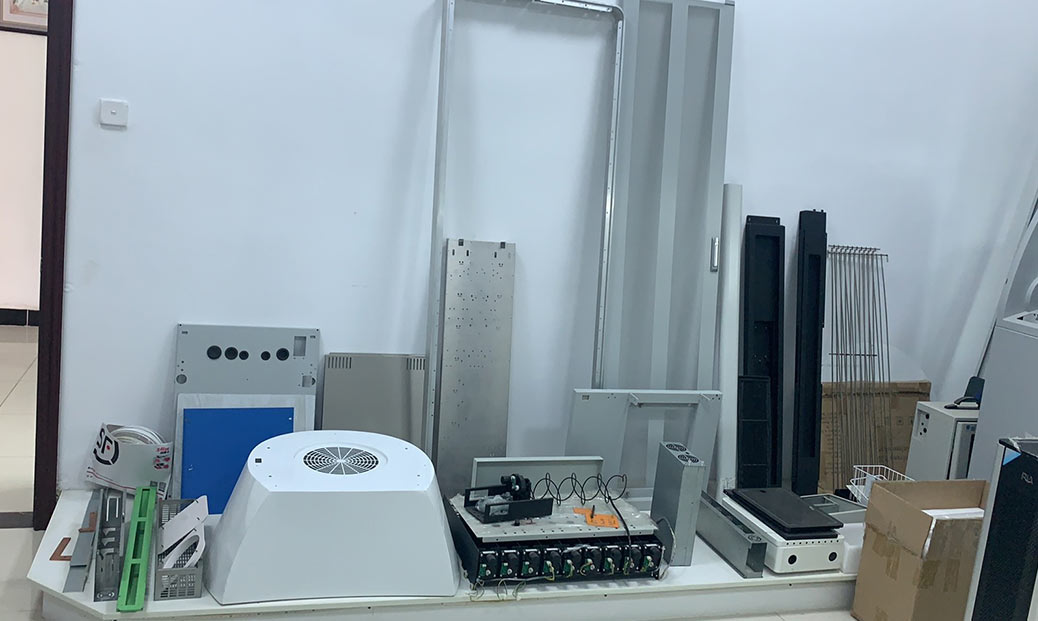