Advantages and disadvantages of cast zinc alloy
Casting zinc alloy has a long production history and is mainly suitable for pressure casting or gravity casting. And in recent years, high-aluminum, high-strength and high-wear-resistant cast zinc alloys have been developed.
After casting, pure metal can become quite hard (eg quenched in water). Commercial zinc contains impurities, so it is brittle and has high hardness. But it can be deformed at temperatures greater than 100°C and can be pressed into sheets or drawn into wire. After being heated to 250°C, the zinc becomes brittle again and can be ground into powder in a bowl. Therefore, the ductility of zinc is related to impurities and temperature. Experiments show that 1.5mm thick pure zinc flakes can basically soften after being kept at 125℃ for half an hour. Due to its low creep resistance, it cannot be used directly for load bearing. Zinc is less ductile than copper, but greater than tin. Zinc containing fine grains is easily rolled. The size of the grains in the metal depends on the cooling conditions. If the melting temperature is high, that is, it exceeds the melting point by a lot, and the cooling is slow, the grains will become coarse.
Like other metals, zinc has the characteristics of work hardening. After mechanical work hardening, it can be annealed at low temperature to restore its ductility.
The critical shear stress of metallic zinc is low, which depends on the strain rate and temperature. Single crystal zinc will bend under its own gravity, and its critical shear stress does not exceed 0.0785MNm-2.
As the temperature increases, the thermal conductivity of zinc decreases, while the specific heat capacity increases. The thermal conductivity of single crystal metal zinc is higher than that of polycrystalline metal zinc. Thermal conductivity varies with crystal orientation. For directionally solidified cast metals, deformation stresses are induced due to anisotropy of thermal expansion.
The resistance of metallic zinc containing impurities is high. The resistance of cold-rolled zinc is slightly larger than that of hot-rolled zinc. The diamagnetism of zinc varies with the crystallographic orientation. Zinc has electrothermal properties, and when the two ends of the zinc sample are placed at different temperatures, an electric current flows inside the sample.
The disadvantage of cast zinc alloy is poor corrosion resistance, and it is prone to aging during long-term use. The aging of the alloy makes the casting brittle and the performance drops sharply. At the same time, the castings are deformed, expanded, and cracked in severe cases. This phenomenon of zinc alloys is generally considered to be mainly caused by intergranular corrosion. The aging of zinc alloys has greatly hindered the wide application of such alloys. Therefore, improving the aging resistance of zinc alloys and preventing and delaying the aging of zinc alloys have become the basic subjects of research and production of such alloys. In our country, zinc is one of the main metals that are mainly developed in the non-ferrous metal industry. Replacing copper alloys and aluminum alloys with zinc alloys is of great significance in saving energy, reducing raw material costs, and rationally using domestic resources.
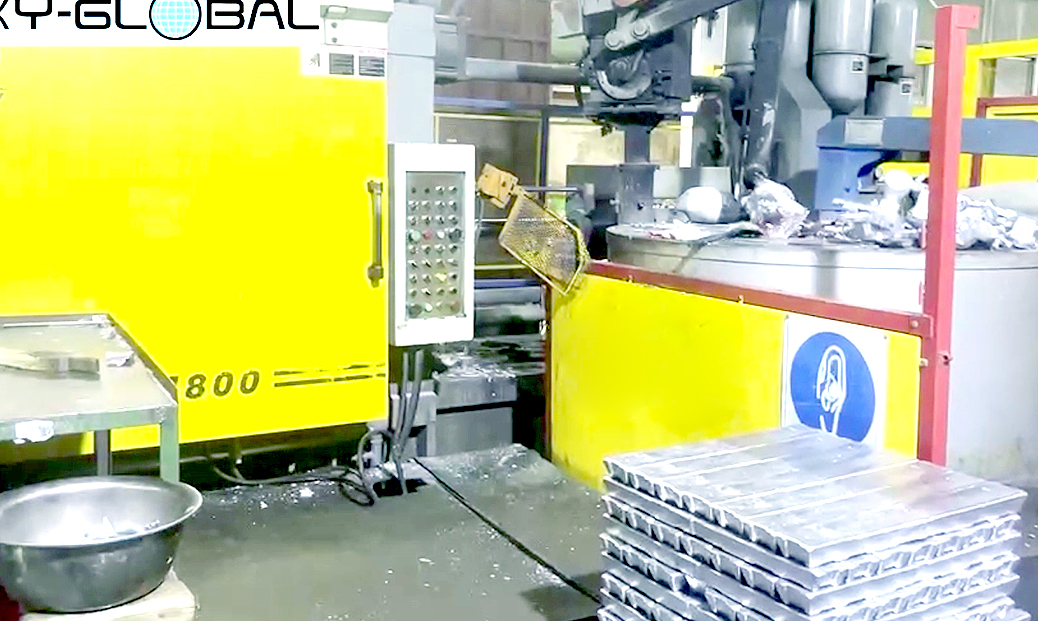